Achieving IN999 purity is a crucial goal in various industries, especially those involved in the production of high-quality alloys and materials. This level of purity indicates that the material contains 99.9% or higher of the desired element, making it essential for applications demanding excellent mechanical and thermal properties. In this article, we will explore innovative techniques and methods employed by industries to achieve in 999 purity, from initial processing to final purification stages. The journey towards achieving this purity level involves numerous intricacies, including material selection, refining processes, and advanced analytical techniques.
Understanding IN999 Purity
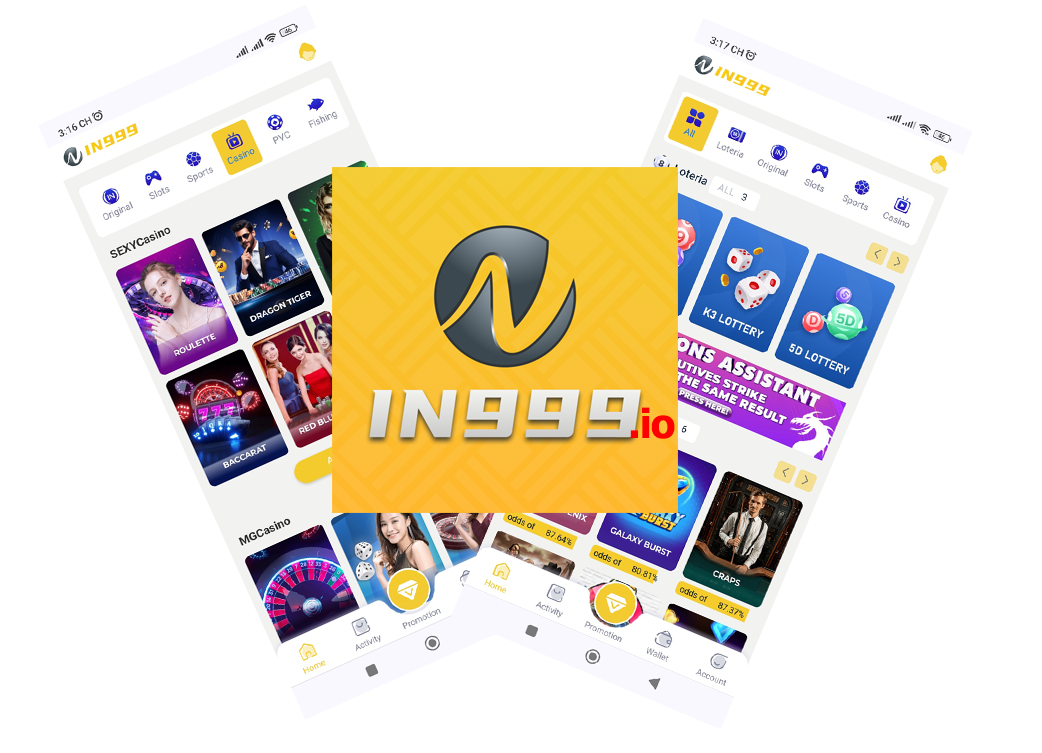
Definition and Importance
IN999 purity refers to the standard of material purity where the concentration of the primary element reaches or exceeds 99.9%. Such levels are essential in high-performance applications ranging from aerospace components to premium consumer electronics. The importance of reaching this purity level cannot be overstated, as impurities can significantly alter the physical and chemical properties of materials, affecting their performance, durability, and overall reliability.
Applications of IN999 Purity
Industries such as aerospace, automotive, and electronics highly demand IN999 purity materials due to their unique attributes, which include enhanced strength, conductivity, and resistance to corrosion. For instance, in the aerospace sector, components made with IN999 pure metals can withstand extreme temperatures and pressures, ensuring safety and operational efficiency. Similarly, electronics manufacturers rely on high-purity materials to produce semiconductors, capacitors, and other critical components.
Challenges in Achieving IN999 Purity
The path to achieving IN999 purity presents several challenges, including contamination from environmental sources, limitations in refining technologies, and difficulties in maintaining consistency throughout production. Understanding these challenges is key to implementing effective strategies and techniques that can help overcome them.
See more: in 999 login
Selection of Raw Materials
Choosing High-Quality Inputs
The foundation of achieving IN999 purity begins with the selection of raw materials. Industries must prioritize sourcing high-quality inputs that are as free from contaminants as possible. This requires establishing relationships with reputed suppliers who adhere to strict quality control measures during extraction and processing.
Understanding Alloy Composition
It is essential to have in-depth knowledge of the alloy composition when selecting raw materials. Each alloy’s grade must be assessed based on its intended application and the level of purity required. This ensures that the selected materials align with industry standards while minimizing the risk of impurities arising from incompatible compositions.
Implementing Rigorous Testing
Before processing raw materials, companies must conduct rigorous testing to ascertain their quality and purity levels. Analytical techniques such as spectroscopy and chromatography can provide insights into the elemental composition and highlight any potential contaminants. By employing advanced testing protocols, businesses can ensure that only materials meeting the required standards enter the production process.
Refining Processes
Mechanical Refinement Techniques
Mechanical refinement plays a vital role in purifying materials to achieve IN999 purity. Techniques such as grinding, milling, and sieving can effectively reduce particle sizes and remove larger impurities. However, it is essential to ensure that these processes do not introduce new contaminants or alter the desired characteristics of the material.
Chemical Refinement Methods
Chemical methods involve the use of various reagents to dissolve or react with impurities, thereby isolating the target element. Techniques such as solvent extraction, precipitation, and electrolysis are commonly employed to enhance purity levels. Each method has its strengths and weaknesses, necessitating careful consideration of the specific impurities present in the raw materials.
Advanced Technologies
Emerging technologies such as plasma melting, vacuum arc remelting, and zone refining offer significant advantages in achieving higher purity levels. Plasma melting, for instance, creates a controlled environment that minimizes contamination risks while allowing for precise temperature management. These advanced techniques often require substantial investments but can yield superior results in terms of purity and material properties.
Quality Control and Analytical Techniques
Establishing Quality Control Protocols
Implementing stringent quality control protocols is paramount for achieving and maintaining IN999 purity. Regular inspections and assessments should be conducted throughout the production process to monitor purity levels and detect any deviations from established standards. This proactive approach helps identify issues early on, preventing compromised batches from reaching the market.
Utilizing Analytical Instruments
Advanced analytical instruments play an invaluable role in assessing material purity. Techniques such as inductively coupled plasma mass spectrometry (ICP-MS) and X-ray fluorescence (XRF) are widely used to analyze samples and quantify impurity levels. By incorporating these technologies into quality control processes, manufacturers can ensure that they consistently meet IN999 purity standards.
Continuous Monitoring and Feedback
Incorporating continuous monitoring systems allows for real-time tracking of purity levels during production. Automated feedback loops can facilitate immediate adjustments to processing parameters, ensuring optimal conditions are maintained. This adaptive approach enhances the ability to respond swiftly to any changes, minimizing the likelihood of producing impure materials.
Environmental Considerations
Managing Contaminants
Environmental factors can contribute significantly to material contamination. Industrial operations must implement measures to mitigate external contaminants, such as dust, moisture, and chemicals. Proper facility design, along with stringent housekeeping protocols, can minimize the exposure of materials to harmful elements during processing and handling.
Waste Management Practices
Responsible waste management practices are essential to achieving IN999 purity. Efforts should be made to recycle and reclaim materials wherever possible, reducing the amount of waste generated during production. This not only contributes to environmental sustainability but also ensures that impurities from waste do not re-enter the production cycle.
Regulatory Compliance
Compliance with environmental regulations is critical in maintaining material integrity. Companies should familiarize themselves with relevant guidelines and standards governing pollutant emissions and waste disposal. By adhering to these regulations, manufacturers can safeguard both their products’ purity and public health.
FAQs
What is IN999 purity?
IN999 purity refers to the standard of material purity where the concentration of the desired element reaches or exceeds 99.9%. It is crucial for applications requiring high-performance characteristics.
Why is achieving IN999 purity important?
Achieving IN999 purity is essential because impurities can adversely affect material properties, compromising performance, durability, and overall reliability, especially in high-stakes industries like aerospace and electronics.
What techniques are used to achieve IN999 purity?
Techniques employed include selection of high-quality raw materials, various refining processes (mechanical and chemical), advanced technologies (plasma melting, vacuum arc remelting), and stringent quality control and analytical techniques.
How can environmental factors affect material purity?
Environmental factors such as dust, moisture, and chemicals can lead to contamination and compromise the purity of materials. Implementing best practices in facility design and housekeeping is necessary to mitigate these risks.
What role does quality control play in achieving IN999 purity?
Quality control is vital in monitoring and maintaining purity levels throughout the production process. Regular inspections, analytical testing, and continuous monitoring systems help ensure compliance with IN999 purity standards.
Conclusion
Achieving IN999 purity is a multifaceted process that demands precision, dedication, and innovative techniques. From the initial selection of raw materials to advanced refining processes and stringent quality control measures, each step plays a critical role in ensuring that the final product meets the highest purity standards demanded by modern industries. As technological advancements continue to develop, the methods for achieving IN999 purity will likely evolve, providing even greater opportunities for innovation and excellence. By understanding and implementing these techniques, industries can enhance their material offerings and position themselves favorably in a competitive marketplace.